OEE: definizione, significato e cos’è
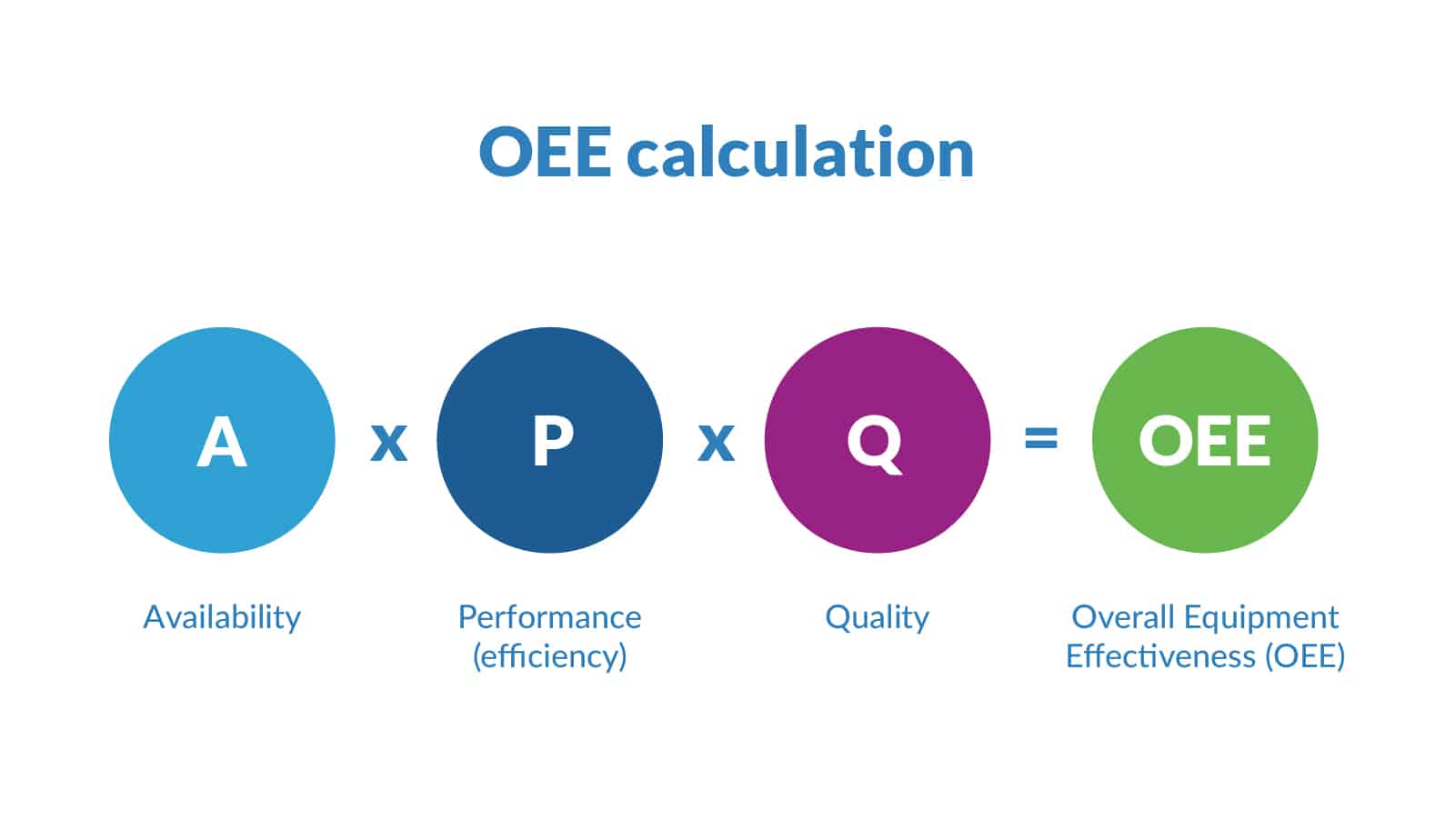
Cos’è OEE: definizione e significato
Contenuti Articolo
OEE è un acronimo inglese. Letteralmente significa “Overall Equipment Effectiveness”, traducibile come “Efficacia complessiva dell’impianto”.
Come suggerisce la sua definizione, si tratta di un indicatore globale e percentuale che misura l’efficienza delle risorse produttive. Queste possono comprendere asset tecnici quanto umani; ad essere misurata è la loro produttività in relazione al tempo disponibile in cui operano.
Quindi, considerato un ammontare di ore, l’OEE indica la percentuale di produzione realizzata rispetto a quella massima possibile in via teorica.
Prendendo ad esempio un caso specifico, consideriamo un totale di 80 ore. Se il calcolo dell’OEE dà un risultato pari a 60%, ciò significa che le risorse impiegate hanno realizzato una produzione che si attesta al 60% rispetto a quella che ottenibile nel determinato lasso temporale.
Quest’informazione risulta essere molto completa e utile in quanto comprende le diverse motivazioni che possono sottendere all’inefficacia produttiva: ad esempio, una pianificazione inadeguata, tempi morti non sfruttati, guasti e avarie.
A cosa serve l’OEE
Come detto nella definizione di OEE, l’utilità di questo indicatore è quella di dare un quadro dell’andamento produttivo. Capire l’effettivo impiego delle risorse disponibili, avere un’idea di cosa dev’essere ottimizzato, comprendere quali sono i fattori che portano ad un deficit produttivo, sono informazioni fondamentali per un sistema di produzione che vuole migliorare la propria efficacia.
Ancor più nello specifico, l’OEE riassume in sé tre fondamentali fattori dal punto di vista della produzione, sempre riferiti ad un intervallo temporale. Essi sono: il tasso di disponibilità dell’impianto, l’efficienza di lavorazione (o prestazione) e il tasso di qualità.
Il primo fattore si riferisce al rapporto tra uptime e downtime. Ciò significa che mette in relazione il tempo in cui un impianto funziona correttamente e ininterrottamente con quello di fermo, dovuto ad esempio a guasti o manutenzione. Tale fattore dell’OEE serve a quantificare la lavorazione effettiva in cui è impiegato l’impianto.
L’efficienza di lavorazione consta in un altro rapporto. Stavolta è messa in relazione la quantità prodotta effettivamente rispetto alla capacità produttiva che sarebbe stata possibile teoricamente. Ciò serve a comprendere e quantificare le micro-fermate dell’impianto che generano un rallentamento causa di inefficienza. Quindi si può capire la velocità con cui un impianto lavora.
Il tasso di qualità indica invece il rapporto tra i pezzi realizzati conformi e il numero di quelli effettivamente prodotti. Ciò serve a comprendere quanto la produzione sia in linea a determinati standard prefissati, ovvero la percentuale di unità in specifica rispetto a tutte quelle prodotte.
L’OEE è lo strumento di misurazione adottato nel Total Productive Maintenance (TPM) e nei programmi di Lean Manufacturing. Quest’indicatore viene usato in quanto serve ad avere un quadro dell’efficacia delle misure adottate, nonché la misurazione dell’efficienza.
Come si calcola l’OEE
Il calcolo dell’OEE è possibile in diversi modi.
Il primo risulta particolarmente adatto a linee di produzione automatizzate, all’industria di processo; la sua difficoltà di applicazione riguarda invece i contesti suddivisi per reparti che producono parti discrete, ovvero pezzi. Ad esempio, nel caso in cui siano presenti più reparti ed essi abbiano macchinari diversi che producono quantità e varietà diverse di beni, l’applicazione di questo modello potrebbe rivelarsi difficoltosa.
Tale modalità di calcolo fa uso dei fattori precedentemente illustrati, ovvero disponibilità, prestazione e qualità.
Ricordiamo che la prima fa riferimento alla percentuale del tempo di attività; la seconda è la percentuale di produzione effettivamente realizzata e ha a che fare con la velocità del lavoro; la qualità è invece quella percentuale che indica le parti conformi prodotte.
Il calcolo dell’OEE, in questo caso, consiste in un’equazione:
OEE= Disponibilità x Prestazione x Qualità
Dove:
- Disponibilità = Uptime / Uptime + Downtime
- Prestazione (o efficienza) = n° di pezzi effettivamente prodotti / n° di pezzi teoricamente da produrre
- Qualità = n° di pezzi realizzati conformi / n° di pezzi prodotti effettivamente
Un’altra possibilità di calcolo dell’OEE risulta maggiormente adatta a contesti produttivi che si compongono di diversi reparti o linee.
In tal caso, il calcolo dell’OEE:
OEE= Tempo redditizio / Tempo disponibile
Dove:
- Tempo redditizio = disponibilità oraria delle risorse; ciò rappresenta l’impegno produttivo di un’azienda e corrisponde all’input.
- Tempo disponibile= tempo standard di lavoro; esso è prestabilito dall’azienda in questione e corrisponde al tempo strettamente necessario per una particolare produzione. In questo caso, è un modo di quantificare l’output.
OEE: vantaggi
L’OEE ha alcuni vantaggi molto significativi per un sistema produttivo che vuol essere efficace ed efficiente al massimo delle sue possibilità.
Con l’introduzione di questo indicatore, è possibile ottenere un’ottimizzazione delle performance attraverso un’adeguata gestione delle risorse: un obiettivo significativo facilmente raggiungibile.
Tant’è vero che i sistemi produttivi che adottano l’OEE si attestano mediamente attorno all’85%, mentre coloro che non l’hanno mai sfruttato raggiungono il 50%.
Per ottenere un risultato così soddisfacente è necessario un continuo monitoraggio e una gestione efficiente delle risorse. Bisogna comprendere quali sono i fattori che penalizzano la produzione e come ovviare a tali circostanze.
Proprio questi sono gli apporti dell’OEE, che si traducono in un vero e proprio vantaggio produttivo.