Magazzino Kan Ban
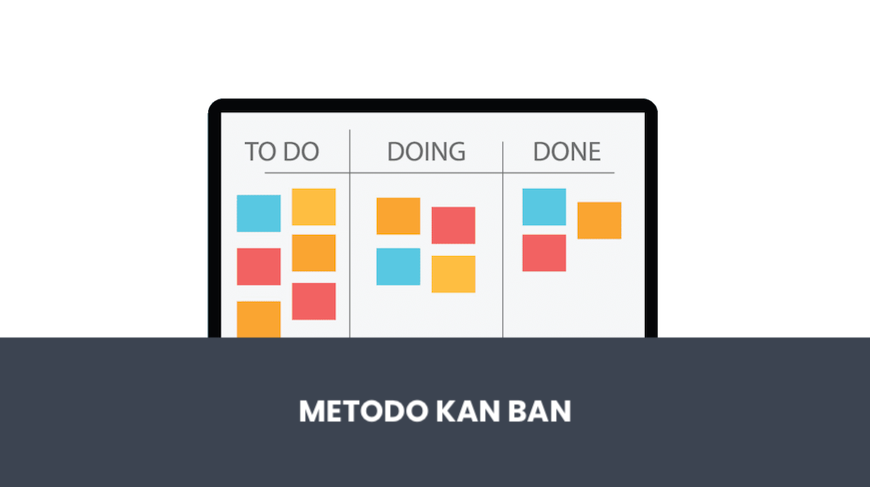
Il magazzino Kanban è tra le soluzioni più efficiente per la supply chain 4.0.
Esso si basa sul concetto che l’ottimizzazione della produzione può essere raggiunta tramite una miglior gestione delle scorte, l’eliminazione di sprechi, l’abolizione della sovraproduzione, l’abbattimento di stagnazione delle attività e la circolazione di informazioni.
Sicuramente, si tratta di fattori che si trasformano in vantaggi competitivi per le aziende, i cui processi vengono considerati come un unico flusso dell’intera supply chain.
Pertanto è utile capirne il significato, il funzionamento, le applicazioni e i software attinenti.
Significato di Kanban: cos’è
Contenuti Articolo
Per capire cos’è il Kanban, è utile riferirsi al suo significato.
Si tratta di un termine giapponese composto da “Kan” (看), ovvero “visuale”, e da “Ban” (板) che significa “segnale”.
Infatti, questo metodo si basa su indicazioni di tipo visivo che servono a segnalare l’avvenuto consumo di materiali e quindi il fabbisogno di rifornimento.
Dunque, tale sistema informativo è atto a controllare gli ordini di produzione e approvvigionamento.
Si tratta di uno dei pilastri portanti del sistema di produzione giapponese e del metodo Toyota, basato sul Just in Time; l’obiettivo di cui si fa portatore è: realizzare solo ciò che è richiesto, quando richiesto e nelle quantità richieste. Nessuno “a monte” deve produrre fino al momento in cui il cliente “a valle” lo richiede.
Dunque, un’attività viene avviata solo nel momento e nelle modalità necessarie, senza alcuno spreco a inficiare sulle performance produttive.
Infatti, il Kanban è una tecnica della Lean Production, ovvero Produzione Snella, che consente di passare da una gestione Push ad una Pull.
Ciò significa che il flusso dei materiali diviene “tirato”: la produzione avviene in base alle reali richieste del mercato, per cui è il cliente finale a determinare la cadenza del flusso produttivo.
Infatti, Ohno (ideatore del pensiero Toyota) suggeriva di pensare al contrario.
Col metodo Kanban è possibile eliminare la sovraproduzione, gli accumuli di scorte e materiali, la stagnazione delle attività.
Al contempo, viene implementata la flessibilità di risposta alla domanda del cliente, viene semplificato il sistema informativo legato alla produzione e viene migliorata l’integrazione dei processi che vanno dal fornitore al cliente.
Ciò comporta una riduzione dei costi e un’ottimizzazione dei tempi, rendendo più efficienti i processi produttivi aziendali.
Il Kanban può essere di due tipi:
- Di movimentazione o trasporto: indicazione per spostare i materiali verso un processo produttivo;
- Di produzione: ordini di produzione per cui al processo a monte viene indicato di avviare la produzione per un processo a valle.
Come detto inizialmente, in riferimento al significato del termine, queste segnalazioni sono visive e avvengono tramite oggetti fisici: i cartellini, che contengono ogni informazione utile a trasportare, acquistare o produrre determinati materiali o componenti. Essi sono posizionati in punti visibili del pallet o del contenitore.
<< Conosci già i requisiti per l’industria 4.0 >>
Come funziona
Per capire come funziona il metodo Kanban, bisogna innanzitutto premettere i tipi di informazione resi disponibili da questi cartellini:
- Il Kanban di movimentazione è collegato ad un ordine di prelievo e si suddivide in semplice e fornitore.
Nel primo il cartellino contiene informazioni utili per lo spostamento dei materiali verso un processo:
- Codice identificativo del materiale
- Descrizione dello stesso
- Quantità di componenti
- Ubicazione
- Numerazione progressiva dei componenti
- Imballo
- Immagine (facoltativa)
Il Kanban fornitore contiene le stesse informazioni più altre aggiuntive che sono utili per il prelievo dal magazzino del fornitore:
- Fornitore del materiale
- Destinazione dello stesso
- Metodi di fornitura
- Il Kanban di produzione, invece, è quello più direttamente collegato alla produzione e si suddivide in tradizionale e segnale.
Il primo è un ordine di produzione e contiene informazioni come:
- Codice identificativo
- Descrizione
- Quantità
- Lavorazione
Il Kanban segnale è il cartellino relativo al riordino, contenente:
- Lead Time, utile per il ripristino delle scorte.
- Codice a barre. Con un lettore scanner il trasferimento di informazioni dal cartellino al sistema ERP viene semplificato.
- Colori, per distinguere più linee di produzione, laddove siano gestite dallo stesso reparto, o per segnalare priorità.
Compreso ciò, è più semplice capire come funziona.
Si consideri la struttura dei processi aziendali come un flusso: ogni sua parte è al contempo un fornitore di quella successiva e un cliente di quella precedente.
Quando quest’ultimo preleva un prodotto dal magazzino, il cartellino ad esso associato viene staccato e inviato a monte del processo.
Chi riceve il Kanban riceve un ordine di movimentazione/acquisto/produzione di quel determinato prodotto, che viene quindi ripristinato e reso nuovamente disponibile; su di esso viene quindi attaccato un nuovo cartellino.
Ciò vuol dire che ogni anello del processo si aziona quando il precedente ne segnala la necessità: vengono eliminate scorte stagnanti e materiali in attesa, ottimizzando il processo complessivo grazie alla comunicazione tra le sue parti. In tal modo, l’intera supply chain diviene molto più efficiente.
Dunque, viene indicato dal cartellino quando e quanto movimentare, acquistare o produrre un certo articolo, in maniera esatta e puntuale.
Oggi i cartellini Kanban si sono digitalizzati, progredendo verso la supply chain 4.0, così da essere gestiti attraverso specifici software.
Software
Il metodo Kanban viene applicato anche nell’ambito dell’Information Technology: un processo di sviluppo software ufficializzato da David J. Anderson nel 2007.
Nel 2010 il metodo viene sdoganato dal libro di Anderson e si diffonde nella produzione di servizi IT, dotandoli di un metodo Agile. Nel 2013 è il software open-source Open Kanban a contribuire ulteriormente alla sua risonanza.
Si tratta di un tool impiegato nel Project Management; consente di capire quanto, come e cosa sta producendo l’azienda in un determinato momento. Fornisce quindi una profonda conoscenza dei processi interni.
Essendo questi ultimi tutti mappati, è possibile avere informazioni utili per compiere azioni solo quando necessario, così da evitare sprechi di tempo e risorse.
Questi tipi di software sono ormai molteplici e molto diffusi nell’industria 4.0.
Tali tools vengono impiegati dai Project Managers in quanto implementano l’organizzazione e l’ottimizzazione dei flussi; consentono la creazione di tragitti, il tracciamento delle attività e la gestione delle tempistiche di ciascuna.
In tal modo, il monitoraggio della produttività conferisce quella snellezza di cui il metodo Kanban si fa portatore.
Infatti, tale metodologia è impiegata nello sviluppo di software in modo da:
- Visualizzare il flusso di lavoro
- Misurare e gestire quest’ultimo
- Fornire politiche di processo trasparenti ed esplicite
- Limitare il Work in process (WIP), ovvero l’immobilizzo di capitale
- Offrire opportunità di miglioramento tramite l’utilizzo di modelli
Il metodo Kanban nel magazzino
Il metodo Kanban viene applicato nel magazzino per ridurre l’accumulo e la giacenza delle scorte, per gli ordini di queste ultime e per l’ottimizzazione dello stoccaggio.
Ciò avviene grazie al supporto di software gestionali aziendali, come il WMS (Warehouse Management System), che consente di gestire in modo digitale e automatizzato ogni attività logistica.
Quando è integrato da codici a barre e RFID (tutte tecnologie di tracciamento e identificazione del prodotto), consente di individuare l’ubicazione di ogni prodotto e le relative informazioni, facilitando la fase di approvvigionamento. Si tratta di ciò che permettono i cartellini: identificazione completa del prodotto, della sua provenienza e della sua destinazione.
Inoltre, il WMS è spesso comunicante con il gestionale ERP e quello MRP, anch’essi aderenti alla logica Kanban e, a loro volta, comunicanti con i cartellini.
Il primo consente la pianificazione delle risorse aziendali, con un’unica struttura integrata di dati che permette la coordinazione dei flussi; il secondo serve a pianificare gli ordini di acquisto e di produzione, programmando il fabbisogno di materiali in base alle richieste (sempre la logica push).
Video sul funzionamento del magazzino Kan Ban
Tutto questo insieme di informazioni integrate permette al WMS di emettere ordini automatici di rifornimento laddove venga segnalata questa necessità. Infatti, se nel magazzino le aree di picking e quelle di stoccaggio sono separate, quando le ubicazioni dedicate alla prima vengono esaurite, avviene automaticamente il rifornimento.
Il WMS per il controllo della produzione, prima di processare un nuovo ordine, invia una notifica all’ufficio acquisti del fornitore per garantire i giusti livelli di stock.
Nel caso di approvvigionamento del retail, gli ordini partono in base alla domanda di un certo prodotto, agevolando la gestione delle scorte.
Duque, il sistema Kanban implementato tramite WMS offre un importante strumento per una gestione integrata e ottimizzata delle scorte, il linea con la Produzione Snella e con il Just in time.
Si tratta quindi di una semplificazione che massimizza l’efficienza, in linea con gli obiettivi e le esigenze dell’industria 4.0.
Infatti, trova adeguata applicazione nel magazzino verticale automatico, che offre automazione proprio grazie ai software gestionali suddetti. La movimentazione e lo stoccaggio delle merci divengono automatiche e più efficienti, consentendo l’ottimizzazione dei flussi e della gestione delle scorte.
Infine, per poter applicare al meglio il metodo Kanban nel magazzino, così da sfruttare le informazioni dei cartellini, è necessario avere alcune accortezze:
- Il pallet contenente i componenti/materiali/prodotti può essere spostato solo se vi è applicato il cartellino;
- Questo deve necessariamente essere affisso su ogni pallet;
- Il cartellino deve contenere sempre lo stesso prestabilito numero di componenti;
- I pallet devono contenere sempre lo stesso prestabilito numero di componenti;
- L’area dedicata ai pallet è fissa e predefinita.