Tolleranze dimensionali
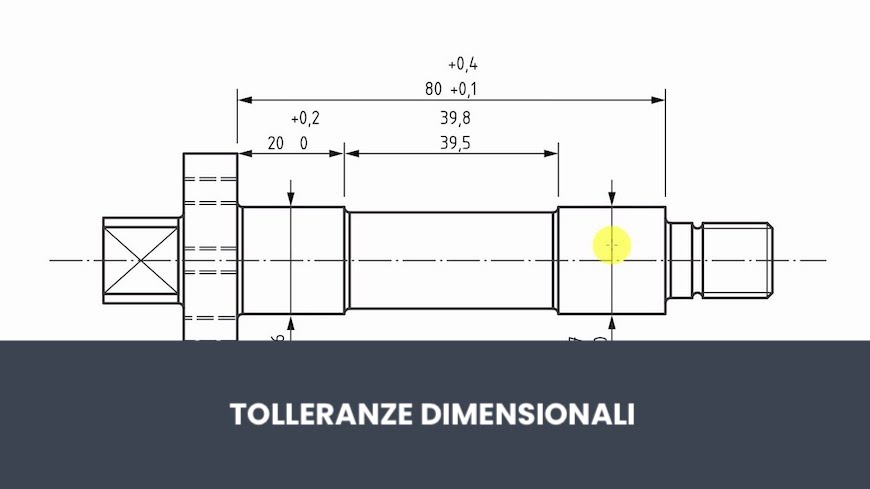
Contenuti Articolo
Vista l’inevitabile imprecisione dei processi di fabbricazione, è importante conoscere le tolleranze dimensionali per poter garantire il funzionamento di determinati componenti. Bisogna quindi sapere cosa sono, quando si usano e perché, per poi approfondire con tabelle e indicazioni per il calcolo.
Tolleranze dimensionali: cosa sono e quando si usano
Per un’indispensabile conoscenza preliminare, occorre innanzitutto comprendere bene cosa sono le tolleranze dimensionali.
Per tolleranza s’intende l’errore massimo che può essere considerato accettabile nella definizione di un certo valore; quest’ultimo può variare, e la tolleranza definisce proprio i limiti ammissibili di tale variazione. I valori in questione possono essere riferiti ad una dimensione o proprietà fisica di un oggetto/sistema/servizio; possono essere relativi alla misurazione di condizioni come: temperatura, tempo o umidità.
Quindi, più nello specifico, la tolleranza dimensionale è il margine accettabile d’errore riferito alle dimensioni di un certo oggetto. Essa viene indicata da una sigla: il numero rappresenta l’intervallo di tolleranza misurato in 𝜇𝑚; la lettera indica la quota minima o massima.
Chiarito cosa sono le tolleranze dimensionali, si può comprendere meglio a cosa servono e quando si usano.
Tutto comincia con la produzione in serie e con la conseguente interscambiabilità tra le parti di un oggetto: ogni pezzo deve poter essere sostituito o assemblato.
Le lavorazioni meccaniche, tuttavia, portano spesso alla circostanza per cui le dimensioni nominali di un oggetto (quelle previste e ideali) non corrispondano a quelle reali ed effettive. Queste inesattezze dimensionali devono essere specificate: entro quali limiti sono ammissibili affinché il pezzo svolga la sua funzione correttamente in relazione ad un altro? Quindi, quanto può variare la dimensione di un componente che dev’essere assemblato ad un altro, senza che ciò vada ad inficiare sul funzionamento complessivo?
Il significato e la funzione delle tolleranze dimensionali risiede proprio in queste domande.
Dunque, la tolleranza dimensionale è un parametro fondamentale che si usa per garantire un giusto accoppiamento tra due componenti, necessario al corretto funzionamento dell’assemblato.
L’albero è il termine convenzionalmente usato per definire un componente pieno (come un perno) e viene indicato con lettere minuscole; il foro si riferisce invece al componente vuoto (ad esempio un foro cilindrico) ed è indicato con lettere maiuscole.
L’accoppiamento può essere di tre tipi, e ciascuno serve a dare informazioni importanti a livello pratico. Quando è mobile (o con gioco), il diametro massimo dell’albero è inferiore a quello minimo del foro; ciò vuol dire che nell’assemblamento l’albero ha possibilità di movimento.
L’accoppiamento con interferenza (o forzato) si verifica quando il diametro minimo dell’albero è maggiore o uguale a quello massimo del foro; ciò significa che il montaggio dell’albero può avvenire solo forzando l’ingresso nel foro.
L’accoppiamento incerto si ha quando nell’assemblaggio si può verificare sia un gioco che un’interferenza; ciò implica che montando l’albero nel foro, il primo o potrà muoversi o rimarrà bloccato.
Tabella delle tolleranze dimensionali
Un’utile tabella delle tolleranze dimensionali è quella riferita al sistema ISO.
Esso prevede 27 posizioni normalizzate di tolleranza rispetto alla linea dello zero, rappresentante le dimensioni nominali, calcolate a partire dall’ampiezza della tolleranza e dalla posizione nel campo di tolleranza (ovvero lo scostamento dalla linea zero, che può essere inferiore o superiore).
Una posizione di tolleranza indica quindi il valore dello scostamento di riferimento ed è indicata con lettere maiuscole per i fori (da A a ZC) e minuscole per gli alberi (da a a zc); ad esempio: F8/h7.
Il sistema ISO, per semplificare le moltissime combinazioni possibili tra posizioni, prevede di mantenere costante la posizione di tolleranza di albero o foro (ponendola come base), facendo variare quella dell’altro elemento. Ecco che si ottengono due sistemi:
Quello albero-base: prevede l’accoppiamento di fori di diverse posizioni di tolleranza con alberi di un’unica posizione di tolleranza (funge da base).
Quello foro-base: viceversa, tiene costante la posizione di tolleranza del foro (base) e fa variare quella dell’albero.
- Una tabella del sistema albero-base:
Posizione dei fori: da A a H | Accoppiamento con gioco |
Posizione dei fori: da Js a N | Accoppiamento incerto |
Posizione dei fori: da P a Zc | Accoppiamento con interferenza |
- Una tabella del sistema foro-base:
Posizione degli alberi: da a a h | Accoppiamento con gioco |
Posizione degli alberi: da js a n | Accoppiamento incerto |
Posizione degli alberi: da p a zc | Accoppiamento con interferenza |
Infine, il sistema ISO prevede 20 gradi normalizzati di tolleranza, indicati con un numero preceduto dalla sigla IT; più piccolo è il numero del grado e minore sarà l’ampiezza della tolleranza ammessa.
- Una tabella delle tolleranze dimensionali (IT) nel sistema ISO, in base alle quali si rendono possibili certi usi e gradi di precisione:
Da IT01 a IT0 | Meccanica di altissima precisione |
Da IT1 a IT4 | Lavorazioni di precisione |
Da IT5 a IT10 | Componenti che devono essere accoppiati, lavorazioni con macchine utensili |
Da IT11 a IT18 | Componenti che non devono essere accoppiati, lavorazioni grossolane |
Calcolo delle tolleranze dimensionali
Per il calcolo delle tolleranze dimensionali bisogna partire da alcuni concetti già toccati:
- Il campo di tolleranza è la differenza tra il valore massimo e quello minimo che può assumere la dimensione di un determinato pezzo. (Dmax – Dmin)
- Lo scostamento è la differenza tra le dimensioni effettive del componente e quelle teoriche (nominali).
Il suo calcolo:
- Lo scostamento superiore (Es) è uguale alla differenza tra la dimensione massima (Dmax) e quella nominale (Dn):
Es = Dmax – Dn
- Lo scostamento inferiore (Ei) è uguale alla differenza tra la dimensione minima (Dmin) e quella nominale (Dn):
Ei = Dmin – Dn
Ogni componente ha un certo grado di precisione (IT), che puoi ritrovare nella tabella sopra, e da cui dipende il campo di tolleranza.
Il grado di precisione viene solitamente assegnato in sede di progetto e, una volta stabilito, si può determinare il valore del campo di tolleranza, in funzione della dimensione nominale.
Per far ciò ci si avvale di semplici tabelle, facilmente accessibili anche tramite web, che mettono in relazione il grado di tolleranza normalizzato (IT) e la dimensione nominale: basta incrociare il valore di riga con quello di colonna per ottenere il valore del campo di tolleranza.
L’operazione successiva è il calcolo dello scostamento del campo di tolleranza dalla linea dello zero. Dall’apposita tabella degli scostamenti si può ricavare il valore di quello inferiore e superiore.
Per concludere il calcolo delle tolleranze dimensionali basta infine definire la dimensione massima e minima, che dipendono dal grado di tolleranza (IT):
Dmax = Dn + Es (dimensione nominale + scostamento superiore)
Dmin = Dn + Ei (dimensione nominale + scostamento inferiore)